|
|
|
 |
|
|
 |
|
Date : 11-01-18 13:39
Fully Automatic Non-Contact Sealing Equipment
|
|
Author :
Lantech
 Views : 1,032
|
Fully Automatic Non-Contact Sealing Equipment
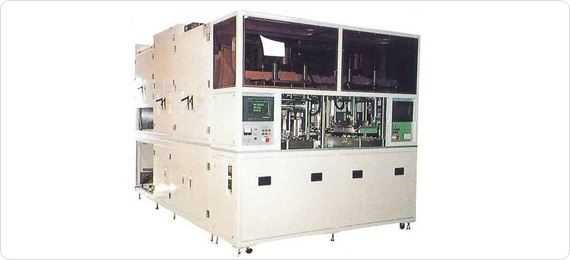
- 1/K2-21-10 for large cells
- As Panel Displays are growing larger in screen size and LCD glass is becoming thinner, the cell gap control in the liquid crystal injection process has grown very difficult. Therefore, cell pressurization and gap control have become essential in the sealing process. Our company has maximized the technologies cultivated through the development and production of contact-type pressurized sealing machines, and developed non-contact pressurized sealing equipment featuring our original LANTEC method.
- LANTEC method
- The non-contact pressurizing system uses air pressure for the adjustment of cell gaps of many cells (standard product specification:40 cells/batch) placed in a pressure tank. It offers a number of outstanding features not offered by the contact-type pressuring system.

-
- 1. Injection and subsequent processes can be automated (use of automatic transfer equipment, shared use of transport jigs).
2. Since air pressure is used for pressurization, extremely uniform cell gap formation is possible, enabling processing of 40 cells per batch. 3. The multiple-pin transfer system used for sealant dispensing can coat 40 cells in a single operation. As a result, the processing time from sealant dispensing to UV irradiation is the same for all cells, thus practically eliminating the problem of chemical reactions between liquid crystals and UV sealant. 4. Since UV sealant is withdrawn into the cells due to pressure reduction, the amount of withdrawn UV sealant is consistent among all cells.

- 1. Sealing jig loading and unloading section
- This section automatically transports the sealing jig positioned in the loader unit to the pressurizing tank.
Insertion and withdrawal of the sealing jig is performed manually by the operator using an MGV. Connection to an AGV is also possible.
- 2. Pressurizing section
- Air pressure supplied by the controlled tank is used to apply pressure simultaneously to the cells set in the cassette in the tank (LANTEC method). It can apply uniform pressure to all cells without contacting.
- 3. Wiping section
- For wiping operation, bemcotton is run parallel to the arranged cells. The wiping operation is repeated during the pressurization and removes excess liquid crystals which are pushed out from cell gaps due to pressure.
- 4. Dispensing of UV sealant section
- The pin transfer system dispenses UV sealant to a set number of cells (standard setting: 40) in a single operation. The pins are designed based on the specified injection hole length. Our standard models can process up to three injection holes per cell.If there are more than three injection holes per cell or if injection hole are located on both ends, please consult our company.
- 5. UV unit section
- After UV sealant is dispensed, UV lights are irradiated to harden the UV sealant and seal the liquid crystal injection holes. By reducing the tank's internal pressure before UV irradiation, UV sealant is withdrawn into the cells, Since the non-contact pressurization method employed by the LANTEC method applies uniform air pressure to all cells, the amount of withdrawn sealant can be controlled precisely.
- Sealing Jig for Non-Contact Pressurized Sealing Equipment
- Various cell sizes can be handled simply by changing the sealing jig.
It is also possible to Process strip and individual cells. For details of sealing jigs and process able cell sizes, contact our sales representative
- Standard pressure reduction program profile
-
1……STEP1.Pressurization starts, pressure rises
2……STEP2.Pressure maintained 3……STEP3.Wiping completed, sealant application begins 4……STEP4.Single-stage pressure reducation 5……STEP5.Lower pressure maintained 6……STEP6.UV irradiation begins 7……STEP7.Pressure lowered 8……STEP8.Pressurization completed
- Two-stage pressure reduction program profile
-
1……STEP1.Pressurization starts, pressure rises
2……STEP2.Pressure maintained 3……STEP3.First-stage pressure reducation 4……STEP4.First-stage Pressure maintained 5……STEP5.Wiping completed, sealant application begins 6……STEP6.Second-stage pressure reducation 7……STEP7.Second-stage Pressure maintained 8……STEP8.UV irradiation begins 9……STEP9.Pressure lowered 10……STEP10.Pressurization completed
|
|
|
|
|
 |
|
|
|
|
|
|
|